Habitat for Humanity of Bulloch County and homeowner to-be Maria Lipsey are hard at work on her house, which is the local Habitat chapter’s 60th but the first to be built using insulating concrete forms, or ICF, construction.
Habitat House 60 a first of its kind
Lipsey’s home, now started, Bulloch’s first using ICF building process; completed House 59 move-in Sunday
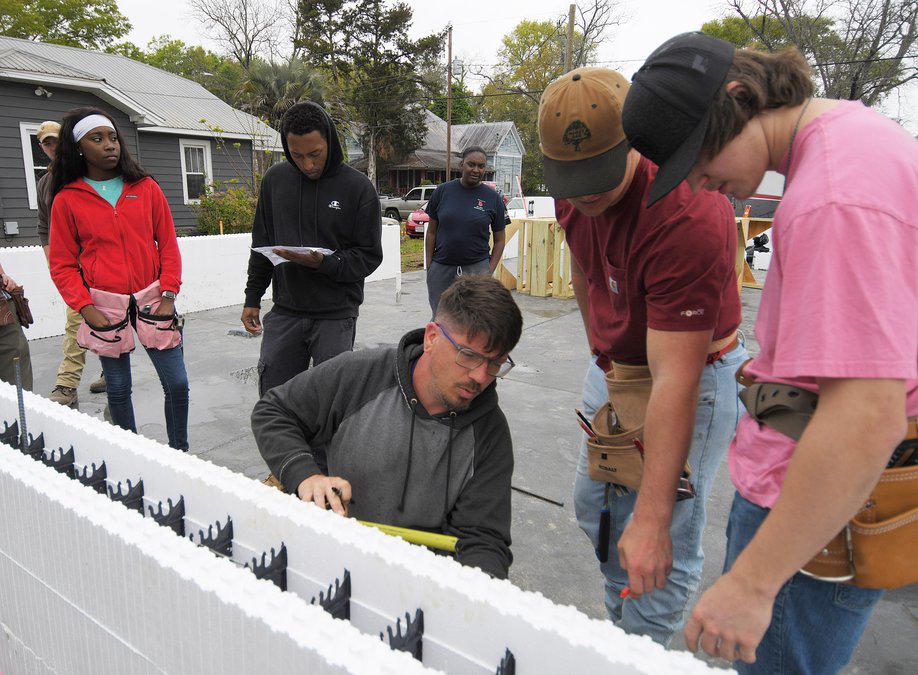
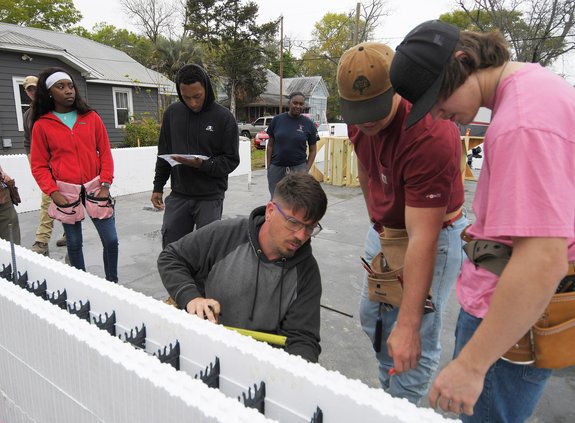
Sign up for the Herald's free e-newsletter